AquaVers™ 405: 5 Million Gallon Potable Water Tank Coating
MARKET: Potable Water : Water Tank Coating Application
SYSTEM: AquaVers™ 405 Elastomeric Pure Polyurea
PROJECT: 5 Million Gallon Water Tank Coating
OWNER: City of Signal Hill – Signal Hill, CA
CONTRACTOR: KC Industries-Kent Hylton-Simi Calley, California
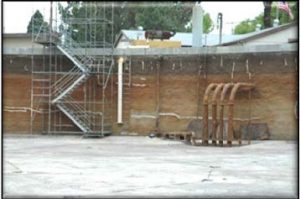
Existing Tank
The following report details the various aspects of the coating application work performed on this five million gallon potable water storage tank. It was determined that the sixty year old subterranean concrete tank was in need of repair and coating. The city decided to utilize a high build elastomeric polyurea coating provided by VersaFlex Incorporated of Kansas City, Kansas. The coating installation was provided by KC Industries of Thousand Oaks, California. The coating application fell into the Thanksgiving holiday, causing some delay. Both the main water tank and sand basin were coated, with the total square footage around 60,000 square feet.
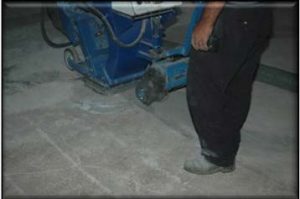
Shot Blasting Surface Preparation
The City of Signal decided to convert an old water basin to storage of potable water. Their vision was to bring the existing structure into compliance with the various governmental regulations leading to recertification of the old tank. Amid other work related to the project, the general contractor installed a metal roofing structure on the tank, then turned the project over to the subcontractor responsible for installing the ANSI/NSF 61.5 compliant interior barrier material.
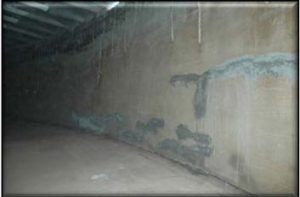
Cracks Repaired
Surface adhesion tests were performed in advance of the coating application to determine the type and degree of surface preparation required. The Sand Basin and main tank walls were prepared using a 3,500 psi high pressure water blast machine. The main tank floor was prepared using a shot blast machine, and any steel structure to be coated was prepared using dry abrasive blast. Large cracks and spalls were repaired with Five Star Structural Concrete. Expansion joints were spanned using a four inch cloth backed butyl tape.
Because of the concrete surface profile, surface cracks and generally irregular surface, the coating specification was designed with an average minimum coating thickness of 80 mils. This allowed continuous coating coverage even on the rougher and more irregular portions of the concrete substrate. Basic requirements for system compliance is 60 mils, but many times surface considerations require more material for proper smoothing of surfaces.
The AquaVers 405 coating was processed through a Graco EXP-2 heated plural component pump, using a Graco Fusion AP spray gun. The Graco pump was also fitted with a data recorder so that critical functions could be recorded to insure proper material processing took place. The pump produced a continuous reading of pump performance. As the project continued, data readings were evaluated to ensure proper operation of the equipment. This data confirmation was included in the final close-out information given to the Owner.
Due to the rapid gel time of the coating (which takes place in seconds), measuring the wet film thickness is not possible. To insure that proper minimum average thickness is achieved, the area to be coated was marked in a grid pattern. Since the spray equipment utilizes a cycle counter to monitor pump output, coating thickness was calculated theoretical coverage rates converted to gallon output. Coating application went in phases, starting first with the main tank walls. After the main tank walls were complete, the contractor moved to the Sand Basin and finally finishing back in the main tank with the floor application.
Critical application conditions were checked and recorded both before and during the coating installation process. The quality assurance checks included surface preparation, concrete moisture content, coating adhesion, ambient conditions, including temperature, humidity, dew point and surface temperature. Since
VersaFlex provided continuous on-site supervision, a NACE Protective Coatings Specialist was not employed . All certifications and testing was undertaken by the manufacturer. It is recommended that NACE or SSPC coating specialists be used when the manufacturer does not offer such service. As industry standards evolve, such specialists will be required to assure Owner satisfaction.
Material processing was recorded by the onboard data recorder, and the entire coating surface was inspected both visually and with the aid of a “Spark Tester” to locate pinholes or thin areas in the coating system.
The condition of the existing tanks was such that repairs and follow-on tank coating was closely monitored for adhesion values. First pulls in each locale were undertaken within hours of coating installation and then attachment of the testing dollies. A delay of 12 to 24 hours was allowed to pass prior to the remaining pull tests.
Subsequent to adhesion testing, test areas were re-prepped and polyurea coating was applied. If adhesion pulls had taken place after installation of completed spraying, this would have proven an additional step, thus testing was undertaken while spray operations were on-going in other tank locations.
After completion of the coating application and prior to the sanitation process, the floor, walls and ceiling were washed to remove overspray dust that had accumulated during the application process.